Simulation H-Beam Stress Analysis
The simulation of an H-beam (stress analysis) in this case study is modeled as a linear elastic material and Hooke's law applies. The computation is carried out statically with the initial geometry created in the CAD software. A distributed load is applied to the upper side of the H-beam, which results in this typical deformation (see figure 4 shown as superelevation).
Although we used a linear elastic material in this case study, the NOGRID software can also compute viscoelastic materials. In contrast to purely elastic bodies, a viscoelastic material has an elastic and a viscous part. The viscosity of a viscoelastic material gives the body a strain rate dependence over time. Purely elastic materials do not dissipate energy when a load is applied and then removed. However, a viscoelastic material dissipates energy when a load is applied and then removed. Viscoelastic behavior has elastic and viscous components modeled as linear combinations of springs and dampers, respectively. Each model differs in the arrangement of these elements. The elastic components can be modeled as springs with elastic constant E given the formula:
σ = Eε
where σ is the stress, E is the elastic modulus of the material, and ε is the strain that occurs under the given stress, similar to Hooke's law. The viscous components can be modeled as dampers, so the relationship between stress and strain rate can be given as:
σ = η dε/dt
where σ is the stress, η is the viscosity of the material, and dε/dt is the time derivative of the strain.
The implemented Maxwell model can be represented by a purely viscous damper and a purely elastic spring connected in series. Under this model, if the material is put under a constant strain, the stresses gradually relax. When a material is put under a constant stress, the strain has two components. First, an elastic component occurs instantaneously, corresponding to the spring, and relaxes immediately upon release of the stress. The second is a viscous component that grows with time as long as the stress is applied.
The implemented Kelvin–Voigt model consists of a Newtonian damper and Hookean elastic spring connected in parallel. This model represents a solid undergoing reversible, viscoelastic strain. Upon application of a constant stress, the material deforms at a decreasing rate, asymptotically approaching the steady-state strain. When the stress is released, the material gradually relaxes to its undeformed state. Without viscous stress (η=0), the material is fully elastic, and only Hooke's law is valid.
In addition, the Generalized Maxwell model, also known as the Wiechert model, is implemented as well and it is the most general form of the linear model for viscoelasticity. It takes into account that the relaxation does not occur at a single time, but at a distribution of times. The Generalized Maxwell model consists of one or more Maxwell elements (viscous damper and elastic spring connected in series), an optional pure viscous, and an optional pure elastic element, all assembled in parallel. One special deduction of the Generalized Maxwell model implemented in NOGRID software is the Tool-Narayanaswamy-Moynihan model.
NOGRID points can be used for designing and problem solving for all kinds of stress related tasks. NOGRID unites abilities to handle stress computations for large deformations and for a lot of viscoelastic materials and allows the simulation of any conceivable geometry and operation modes such as
- computation is in full 3D solving viscoelastic material behavior
- easy and intuitive setup
- free definable material properties by User equations or User curves
- Structure-Structure Interaction with viscoelastic materials
- Fluid-Structure Interaction using all viscoelastic models implemented
- computation of moving parts or moving boundaries in combination with viscoelastic materials
Nogrid's strengths
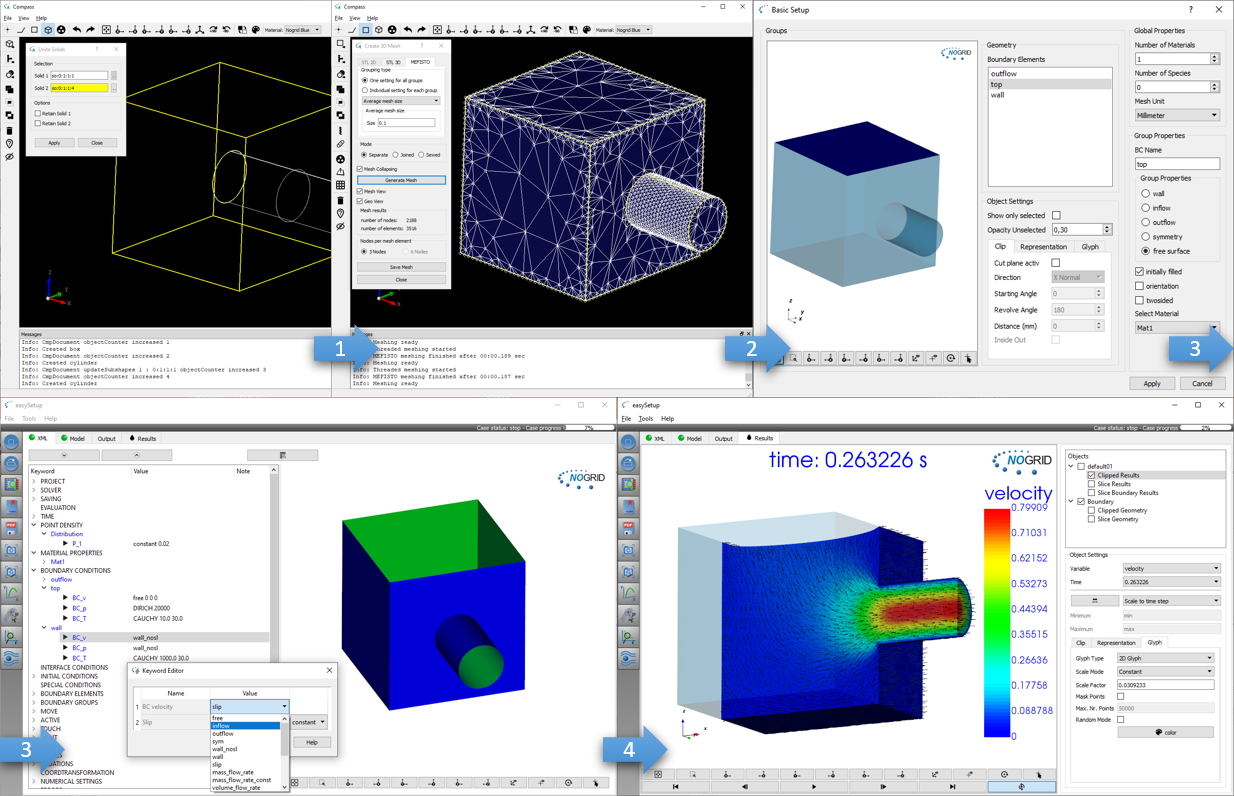
Easy and fast modelling: Build geometry, mesh boundary, setup the case and start computation
What is CFD from NOGRID?
CFD solves the fundamental equations that define the fluid flow process. With CFD software from NOGRID every engineer makes better decisions by predicting, analyzing and controlling fluid flow, heat and mass transfer or chemical reaction. By using NOGRID software for flow modeling you receive information on essential flow characteristics as for example flow distribution. Using it additional to testing and experimentation NOGRID software helps to improve the evaluation of your design – resulting in better construction and operation parameters, increasing planning security and money savings due to faster time to the marketplace for your product or process.
Choose NOGRID
With NOGRID, you choose professional CFD software and services – our aim is helping you to be successful. When you decide to work with NOGRID you choose close cooperation with a dynamic, flat hierarchies-organization. Short information channels result in quick and accurate professional support and service. Our team consists of highly qualified employees, who are experts in fields such as numerical simulation or computational fluid dynamics. Based on our know-how, we are pleased to offer the following services, responding to your individual requirements:
TRAINING
In our two-days training courses you will learn, how to use NOGRID CFD software efficiently. Our technical support team will teach you how to handle and solve different cases.
For more details please refer to Training Courses →
Technical Support
We offer full professional support from the minute you start using our software, by telephone or by email. Contact us, when ever needed.
For more details please refer to Software Support →
Service
Lack of time or resources and other constraints often make outsourcing an attractive solution. We help you with your flow modeling needs. Based on our engineering expertise in this field we offer individual numerical simulation services matching the unique needs of your organization.
For more details please refer to Simulation Services →