Simulation of three Refrigerator PUR Filling and Foaming Processes
Figure 1: PUR refrigerator: Filling process is a mixure of initial pressing and foaming
Figure 2: Refrigerator foaming with moving needle as injector
Figure 3: Refrigerator PUR foam filling with two inlets
Figure 4: Air entrapment generation, velocity field and free surface flow near cooling cutouts, computed with NOGRID points
In this case study we present the simulation of three possible refrigerator PUR filling and foaming processes (injection types), even if not all are in productive use:
In the left top example (figure 1) the simulation starts with PUR liquid inside an open cavity. The cavity closes and presses the foaming liquid into the refrigerator wall.
In the middle example the fluid is injected by a pipe which moves outwards during the filling process.
The left bottom example shows a refrigerator where the PUR is injected using two inlets at the lower side. The foaming process starts when the PUR enters the cavity, the filling is done after two seconds.
Simulate any conceivable refrigerator geometry
- computation is in full 3D solving complete Navier-Stokes-Equations
- easy and intuitive setup of the FSI (Fluid-Structure-Interaction) case
- free definable PUR material properties by equations or curves
- polyurethane (PUR) injection by one or more inlets
- open or closed domains including moving of additional parts
- moving of the mixing head
Nogrid's strengths
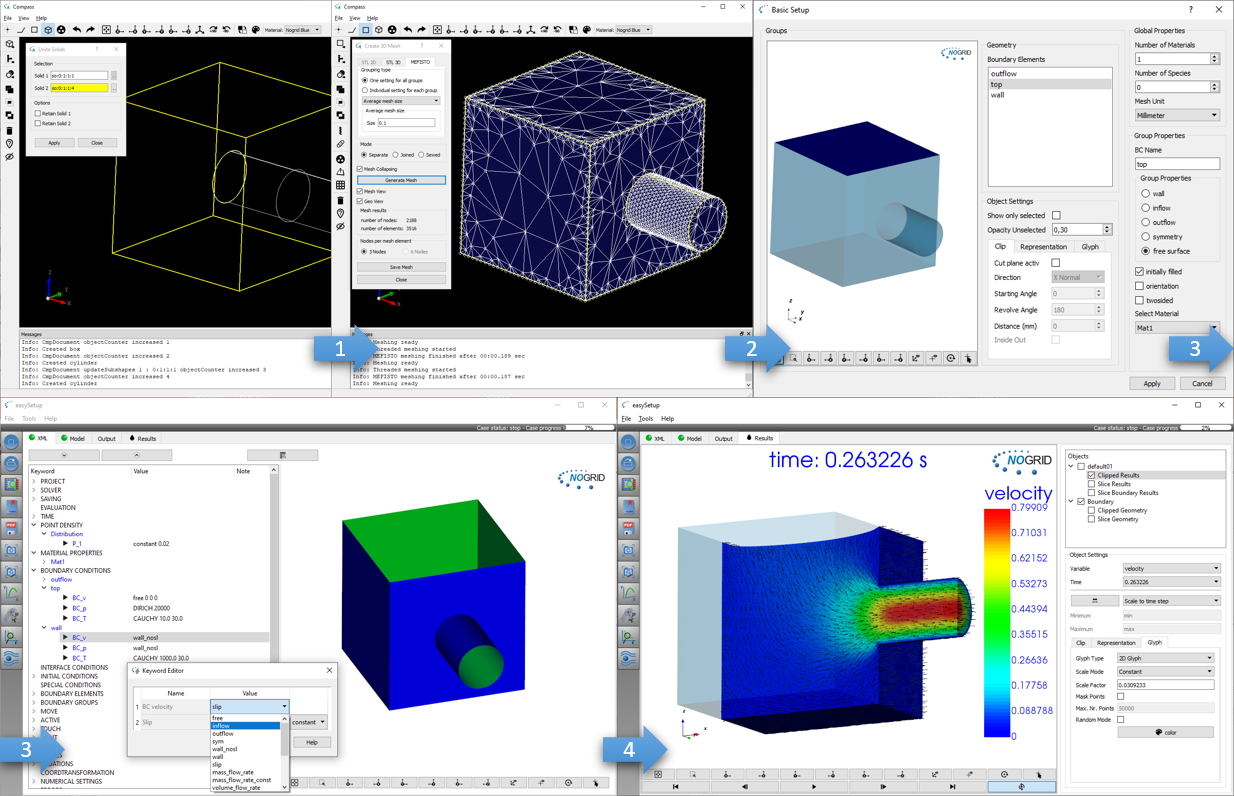
Easy and fast modelling: Build geometry, mesh boundary, setup the case and start computation
What is CFD from NOGRID?
CFD solves the fundamental equations that define the fluid flow process. With CFD software from NOGRID every engineer makes better decisions by predicting, analyzing and controlling fluid flow, heat and mass transfer or chemical reaction. By using NOGRID software for flow modeling you receive information on essential flow characteristics as for example flow distribution. Using it additional to testing and experimentation NOGRID software helps to improve the evaluation of your design – resulting in better construction and operation parameters, increasing planning security and money savings due to faster time to the marketplace for your product or process.
Choose NOGRID
With NOGRID, you choose professional CFD software and services – our aim is helping you to be successful. When you decide to work with NOGRID you choose close cooperation with a dynamic, flat hierarchies-organization. Short information channels result in quick and accurate professional support and service. Our team consists of highly qualified employees, who are experts in fields such as numerical simulation or computational fluid dynamics. Based on our know-how, we are pleased to offer the following services, responding to your individual requirements:
TRAINING
In our two-days training courses you will learn, how to use NOGRID CFD software efficiently. Our technical support team will teach you how to handle and solve different cases.
For more details please refer to Training Courses →
Technical Support
We offer full professional support from the minute you start using our software, by telephone or by email. Contact us, when ever needed.
For more details please refer to Software Support →
Service
Lack of time or resources and other constraints often make outsourcing an attractive solution. We help you with your flow modeling needs. Based on our engineering expertise in this field we offer individual numerical simulation services matching the unique needs of your organization.
For more details please refer to Simulation Services →